Investigation of the Effect on Surface Roughness of Cryogenic Process Applied to Cutting Tool
Furgan BAYRAKTAR and Fuat KARA,
Volume 7: Issue 2, July 2020, pp 19-27
Author's Information
Fuat KARA2
Corresponding Author
2Associate Professor, Düzce University Düzce / Turkey.
fuatkara@duzce.edu.in
Furgan BAYRAKTAR1
1Master Student, Düzce University Düzce / Turkey.
Abstract:-
As the cryogenic treatment is the most harmless mechanical healing process in terms of both environmentally friendly and human health, its usage is increasing day by day. In this study, the effect of deep cryogenic process applied on cutting tool material on surface roughness parameters will be investigated. In this context, Sleipner cold work tool steel will be used as workpiece material and PVD (physical vapour decomposition) coated carbide tools will be used as cutting tool. Cutting tool material will be deep cryogenic at -180 °C. A total of 36 cutting tests will be performed for two different cutting tools (untreated, treated) in three different cutting speeds (40, 60, 80 m/min) and three different feed rates (0.04, 0.06, 0.08 mm/rev) combinations. In this study, Taguchi analysis was applied to experimental data. However, analysis of variance, linear and multiple regression analysis were performed. As a result, the effect of the cryogenic process applied to the cutting tool material was examined both experimentally and statistically.Index Terms:-
Cryogenic process, sleipner, surface roughness, carbide toolREFERENCES
[1] F. Kara, Investigation of the effects of cryogenic treatment parameters on fatigue life and grindability of AISI 52100 steel. Diss. Ph. D. Thesis, Karabük University, 2014.[2] P. K. Wright and E. M. Trent, Metal Cutting. Butterworth-Heinemann, 2000.
Crossref
[3] S. S. Gill, R. Singh, H. Singh and J. Singh, Wear behaviour of cryogenically treated tungsten carbide inserts under dry and wet turning conditions. International Journal of Machine Tools and Manufacture, vol. 49, no. 3-4, pp. 256-260, 2009.
Crossref
[4] D. Mohan Lal, S. Renganarayanan and A. Kalanidhi, Cryogenic treatment to augment wear resistance of tool and die steels. Cryogenics, vol. 41, no. 3, pp. 149-155, 2001.
Crossref
[5] F. Kara, “Optimization of surface roughness in finish milling of AISI P20+ S plastic-mold steel,” Materials and Technology, vol. 52, no. 2, pp. 195–200, 2018.
Crossref
[6] G. Taguchi, S. Chowdhury and Y. Wu, ‘Taguchi's Quality Engineering Handbook’ John Wiley & Sons Inc.: New Jersey, USA, ISBN: 978-0-471-41334-9, 2005.
Crossref
[7] E. Nas and N. A. Özbek, Optimization of the machining parameters in turning of hardened hot work tool steel using cryogenically treated tools. Surface Review and Letters (SRL), vol. 27, no. 5, pp. 1-14, 2020.
Crossref
[8] F. Kara, Optimization of cutting parameters in finishing milling of Hardox 400 steel. International Journal of Analytical, Experimental and Finite Element Analysis (ijaefea), vol. 5, no. 3, pp. 44-49, 2018.
Crossref
[9] O. Özbek and H. Saruhan, The effect of vibration and cutting zone temperature on surface roughness and tool wear in eco-friendly MQL turning of AISI D2. Journal of Materials Research and Technology. vol. 9, no. 3, pp. 2762-2772, 2020.
Crossref https://doi.org/10.1016/j.jmrt.2020.01.010.
[10] A. K. Sahoo and B. Sahoo, A comparative study on performance of multilayer coated and uncoated carbide inserts when turning AISI D2 steel under dry environment. Measurement, vol. 46, no. 8, pp. 2695-2704, 2013.
Crossref
To view full paper, Download here
To View Full Paper
For authors
Author's guidelines Publication Ethics Publication Policies Artical Processing Charges Call for paper Frequently Asked Questions(FAQS) View all Volumes and IssuesPublishing with
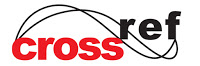
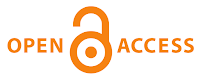
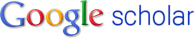
