Enhancing the Performance of Turbine Blades through CAD-Based Design Optimization and Finite Element Analysis: A Comprehensive Review
Bhupesh Sonkar, Amit Sarda, Robin Babu
International Journal of Analytical, Experimental and Finite Element Analysis
Volume 10: Issue 2, June 2023, pp 35-37
Author's Information
Bhupesh Sonkar1
Corresponding Author
1Christian College of Engineering and Technology, Bhilai, India
bhupeshsonkar@gmail.com
Amit Sarda2
2Christian College of Engineering and Technology, Bhilai, India
Robin Babu3
3Christian College of Engineering and Technology, Bhilai, India
Abstract:-
Turbine blades play a critical role in the efficient operation of power generation systems, aircraft engines, and gas turbines. With the aim to enhance their performance, researchers have been utilizing computer-aided design (CAD) and finite element analysis (FEA) techniques to optimize the design of turbine blades. This paper presents a comprehensive review of the recent advancements in CAD-based design optimization and FEA techniques for improving the performance of turbine blades. The review covers various aspects of turbine blade optimization, including aerodynamic performance, structural strength, and vibration characteristics. Additionally, the review discusses the challenges and limitations of the current optimization techniques and suggests future research directions. Overall, this review aims to provide insights into the current state-of-the-art of turbine blade design optimization and to stimulate further research in this field.Index Terms:-
Turbine blade, CAD, Finite element analysis, Design optimization, Performance enhancement..REFERENCES
- International Technology Roadmap for Semiconductors (ITRS), Heterogeneous Integration Chapter, http://www.itrs2.net/
- John H. Lau, “Recent Advances and Trends in Fan-Out Wafer/Panel-Level Packaging”, J. Electron. Packag., Hongkong, vol. 141, May 2019.
- R. Mahajan et al., "Embedded Multidie Interconnect Bridge—A Localized, High-Density Multichip Packaging Interconnect," IEEE Transactions on Components, Packaging and Manufacturing Technology, vol. 9, no. 10, pp. 1952-1962, Oct 2019.
- J. H. Lau, "Recent Advances and Trends in Advanced Packaging," in IEEE Transactions on Components, Packaging and Manufacturing Technology, vol. 12, pp. 228-252, Feb. 2022.
- Murayama, Kei, et al., “Warpage control of silicon interposer for 2.5D Package Application,” IEEE 63rd Electronic Components and Technology Conference, Las Vegas, NV, USA, pp. 879-884, May 2013.
- Shao, Shuai, et al., “Comprehensive study on 2.5D package design for board-level reliability in thermal cycling and power cycling,” 68th Electronic Components and Technology Conference(ECTC), San Diego, CA, USA, pp. 1668-1675, May 2018.
- Il-Woong Suh, et al., “Thermal Analysis of 3D package using TSV Interposer,” Journal of Microelectronics and Packaging, vol. 20, pp. 43-51, 2014.
- Choi Sumin, et al., “Crosstalk-Included eye diagram estimation of high-speed and wide I/O interposer channel for 2.5D/3D IC,” IEEE 23rd Conference on Ele ctrical Performance of Electronic Packaging and Systems, Portaland, OR, USA, pp. 215-218, October 2014.
- You, Jhih-Wei, et al., “Performance characterization of TSV in 3D IC via sensitivity analysis,” IEEE 19th Asian Test Symposium, Shanghai, China, pp. 389-394, December 2010.
- Kim, Joohee, Jonghyun Cho, and Jongho Kim. “TSV modeling and noise coupling in 3D IC,” IEEE 3rd Electronics System Integration Technology Conference ESTC, Berlin, Germany, pp. 1-6, September 2010.
- Junsung Ma, Sarah Eunkung Kim, and Sungdong Kim. “The effects of Cu TSV on the Thermal Conduction in 3D stacked IC,” Journal of the Microelectronics and Packaging Society, vol. 21, pp. 63-66, 2014.
- Lin, Yi-Hang, et al., “Multilayer RDL interposer for heterogeneous device and module integration,” IEEE 69th Electronic Components and Technology Conference (ECTC), Las Vegas, NV, USA, pp.931-936, May 2019.
- Lee, Hyunsuk, et al., “Electrical performance of high bandwidth memory(HBM) interposer channel in terabyte/s bandwidth graphics module,” IEEE International 3D Systems Integration Conference (3DIC), Sendai, Japan, pp. TS2. 2.1 -TS2. 2.4, August 2015.
- Jung, Cheong-Ha, Amit Sarda, and Robin Babu. “Parasitic efeect analysis in TSV design factors,” IEEE 24th Electronics Packaging Technology Conference (EPTC), Singapore, pp. 249-251, December 2022.
- Sunohara, Masahiro et al., “Studies on electrical performance and thermal stress of a silicon interposer with TSVs,” Proceedings 60th Electronic Components and Technology Conference (ECTC), pp. 1088-1093, June 2010.
- EN Abramova, et al., “Porous silicon for drug delivery systems,” Journal of Physics: Conference Series, April 2017.
To view full paper, Download here .
To View Full Paper
For authors
Author's guidelines Publication Ethics Publication Policies Artical Processing Charges Call for paper Frequently Asked Questions(FAQS)Publishing with
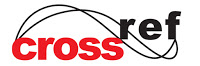
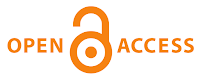
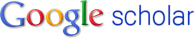
