Improvements in Productivity and Quality for Ductile Iron Flange Castings Using Simulation Technique
Sumit Mathur, Srinivasa Rao Pulivarti
Journal of Production and Industrial Engineering
Volume 3: Issue 2, October 2022, pp 15-20
Author's Information
Srinivasa Rao Pulivarti1
Corresponding Author
1Mechanical Engineer, Quality check Department, RITES Limited, C.G, India
srinivas.indore@e-mail.com
Sumit Mathur2
2Mechanical Engineer, Quality check Department, RITES Limited, C.G, India
Abstract:
An important element of the automobile manufacturing process involves the utilization of foundries. Today's foundries' quality and output are low because of variations in the casting process's many variables. The solidification procedure following pouring is crucial to the final quality of the casting. In order to plan the casting process for making castings before castings are produced or before new or better equipment is built, foundries are increasingly turning to computerized casting modelling and solidification simulation. With the use of computerized casting modelling and solidification simulation, manufacturers may improve the quality of their castings at a lower cost, without sacrificing quantity. As a result of casting solidification simulation, the number of trials performed on the shop floor may be cut significantly, and defect-free castings can be guaranteed. Finite element method (FEM), finite difference method (FDM), and finite volume method (FVM) are the theoretical basis of the casting simulation methods (FVM). In this study, we explore the application of the finite difference method (FDM) and the finite volume method (FVM) to simulate the solidification of a casting and to optimise the casting gating system for maximum yield. This research looks at how modelling and simulation can help improve our understanding of Flange. Flanges are made of ductile iron using a shell moulding method. Mechanically, ductile iron may be used to make a variety of vehicle components.Index Terms:
Ductile iron, Casting modeling, Simulation, Optimization of gating system, Yield optimization..REFERENCES
- J. O. Choi, J. Y. Kim, C. O. Choi, J. K. Kim, and P. K. Rohatgi, “Effect of rar earth element on microstructure formation and mechanical properties of thin wall ductile iron castings,” Mater. Sci. Eng. A, vol. 383, no. 2, pp. 323–333, 2004.
Crossref - W. Xu, M. Ferry, and Y. Wang, “Influence of alloying elements on as-cast microstructure and strength of gray iron,” Mater. Sci. Eng. A, vol. 390, no. 1–2, pp. 326–333, 2005.
Crossref - K. M. Pedersen and N. S. Tiedje, “Graphite nodule count and size distribution in thin-walled ductile cast iron,” Mater. Charact., vol. 59, no. 8, pp. 1111–1121, 2008.
Crossref - K. Herfurth and S. Scharf, “Casting,” Springer Handbooks, pp. 325–356, 2021.
Crossref - T. Willidal, W. Bauer, and P. Schumacher, “Stress/strain behaviour and fatigue limit of grey cast iron,” Mater. Sci. Eng. A, vol. 413–414, pp. 578–582, 2005.
Crossref - R. Salazar F., M. Herrera-Trejo, M. Castro, J. Méndez N., J. Torres T., and M. Méndez N., “Effect of nodule count and cooling rate on as-cast matrix of a Cu-Mo spheroidal graphite,” J. Mater. Eng. Perform., vol. 8, no. 3, pp. 325–329, 1999.
Crossref - T. Skaland, “Developments in Cast Iron Metallurgical Treatments,” pp. 1–29, 2001.
- D. White, “Avoiding Shrinkage Defects and Maximizing Yield in Ductile Iron,” Trans. Am. Foundry Soc., vol. 120, no. 12–081, pp. 389–398, 2012.
- Z. IGNASZAK, “The Risk of Ductile Iron Post-inoculation for Heavy Section Castings,” Mater. Sci., vol. 9, no. 3, pp. 245–249, 2003.
To view full paper, Download here
To View Full Paper
For authors
Author's guidelines Publication Ethics Publication Policies Artical Processing Charges Call for paper Frequently Asked Questions(FAQS) View All Volumes and IssuesPublishing with
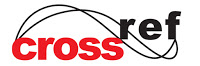
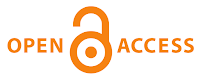
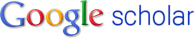
