Optimization of Cutting Parameters in Finishing Milling of Hardox 400 Steel
Fuat KARA
Volume 5: Issue 3, Oct 2018, pp 44-49
Author's Information
Fuat KARA1
Corresponding Author
1Düzce University, Technology Faculty, Department of Mechanical and Manufacturing Engineering, 81620, Düzce, Turkey.
fuatkara@duzce.edu.tr
Abstract:-
In this study, it was performed to optimization of cutting parameters in finishing milling of Hardox 400 steel with PVD TiAlN+TiN coated carbide inserts. Milling experiments were made according to Taguchi L16 orthogonal array. The evaluation of the experimental results was based on the signal/noise (S/N) ratio. Control factors that given optimum surface roughness values were determined by using the Taguchi method. Two different cutting speeds (60 and 120 m/min) and cooling method (dry and wet) as control factors was selected. In addition, depth of cut and feed rate were taken as 0.3 mm and 0.1 mm/rev, respectively. The effect levels on the surface roughness of the control factors with analysis of variance (ANOVA) performed using the experimental results were determined. The Taguchi analysis found the optimum results for surface roughness to be with the cutting speed of 120 m/min and cooling method of wet.Index Terms:-
Finishing milling, Hardox 400, Taguchi method, surface roughnessREFERENCES
[1] J. Majerik and J. Jambor,―Hard milling and hard drilling experiment of abrasion resistant steel Hardox 500 at dependence of T = f (vc, fz),‖Univ Rev.,vol. 8(3-4), pp. 2-8, 2014.[2] J.Majerik and I. Barenyi, ‗Experimental investigation into tool wear of cemented carbide cutting inserts when machining wear resistant steel Hardox 500,‖Eng Rev.,vol. 36(2),pp. 167-174, 2016.
[3] G. Taguchi, S. Chowdhury and Y. Wu, ‗Taguchi's Quality Engineering Handbook‘John Wiley & Sons Inc.: New Jersey, USA, ISBN: 978-0-471-41334-9, 2005.
[4] M. Karabatak and F. Kara, ―Experimental optimization of surface roughness in hard turning of AISI D2 cold work tool steel,‖J Polytech.,vol. 19(3), pp. 349-355, 2016.
[5] N. AltanÖzbek,―The Investigation of the Effects of Cryogenic Treatment Applied to Cutting Tools on Tool Life in Machining AISI 316 Austenitic Stainless Steel,‖ Ph.D. Thesis, Gazi University Institute of Sciences, 2013.
[6] F. Kara, ―Optimization of surface roughness in finish milling of AISI P20+ S plastic-mold steel,‖ Mater Technol., vol. 52(2), pp. 195–200, 2018.
[7] F. Kara, ―Taguchi optimization of surface roughness and flank wear during the turning of DIN 1.2344 tool steel,‖Mater Test.,vol. 59(10), pp. 903-908, 2017.
[8] E. Nas and B. Öztürk, ―Optimization of surface roughness via the Taguchi method and investigation of energy consumption when milling spheroidal graphite cast iron materials,‖Mater Test.,vol60(5), pp. 519-525. 2018.
[9] F. Kara and B. Öztürk, ―Comparison and optimization of PVD and CVD method on surface roughness and flank wear in hard-machining of DIN 1.2738 mold steel,‖Sensor Rev.,https://doi.org/10.1108/SR-12-2017-0266, in press, 2019.
[10] E. Yücel and M. Günay, ―Modelling and optimization of the cutting conditions in hard turning of high-alloy white cast iron (Ni-Hard),‖Proc Inst MechEng Part C: J MechEng Sci.,vol. 227(10), pp. 2280-2290, 2013.
[11] O.Özbek and N. AltanÖzbek, ―Application of Taguchi method in the optimization of cutting parameters for surface roughness in turning of hardened AISI 4140 steel,‖J AdvTechnol Sci.,vol. 5(3), pp. 41-48, 2016.
[12] E. Yücel and H. Saruhan,―Design optimization of rotor-bearing system considering critical speed using Taguchi method,‖Proceedings of the Institution of Mechanical Engineers, Part E: J Process Mech Eng., vol. 231(2), pp. 138-146, 2017.
To view full paper, Download here
To View Full Paper
For authors
Author's guidelines Publication Ethics Publication Policies Artical Processing Charges Call for paper Frequently Asked Questions(FAQS) View all Volumes and IssuesPublishing with
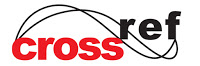
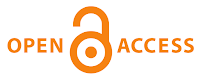
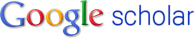
