Productivity Improvement of Metal Casting Industry
Aniruddha Joshi, Prof.L.M.Jugulkar
Volume 1: Issue 3, July 2014, pp 179-183
Author's Information
Aniruddha Joshi1
Corresponding Author
1Student of M-Tech Automobile Engineering, Rajarambapu Institute of Technology, Islampur, Maharashtra, India
aditya3909@gmail.com
Prof.L.M.Jugulkar2
2Faculty of Automobile Engineering, Rajarambapu Institute of Technology, Islampur, Maharashtra, India
Abstract:-
Metal Casting is the process of foundry which has capacity to produce discrete output from raw material. Productivity of metal casting process is nothing but rate of overall production of one organization. Metal Casting process involves pattern making, core making, sand preparation, mold making, melting, pouring and shakeout activities. Several organizations in India followed manual operations to perform these activities. This paper represents the data of manual metal casting operations collected from one organization which produces automotive components. There are various problems identified in industry, low productivity, manual heavy operations, ergonomic problems, ineffective plant layout, process flow problem are represented in this paper. So it is clear from collected data that it affects on profit of organization. The work is done for minimization of these problems. The paper represents solutions, effective plant layout, automatic mold making operation and sequential process flow with minimization of back flow of material helps to solve these problems. The work done is to improve productivity and profit of industry. So this paper represents solution for improvement in productivity and profit of organization..Index Terms:-
Productivity, Plant layout, Ergonomics, Process flow, Manual operations, effective plant layout, Automation for mold making, Sequential flow of operation.REFERENCES
- Peter Beeley, (2001), “Foundry technology”, Butterworth –Heinemann publication. Second edition, ISBN 07506-45679.
- Sukanto Bhattacharya, Australia (2002) “Optimal Plant Layout Design for Process-focused Systems”, School of Information Technology Bond University, 1-13.
- Mayank Singh, Raval Apurv J. (2004), “Life cycle analysis of conventional Manufacturing techniques: Sand casting, Proceeding of ASME International mechanical engineering congress and exposition, pp-705-715.
- Emmanuel Brousseau and Eldaw Eldukhri, (2009), “Recent advances on key technologies for innovative manufacturing”, Springer publication, pp-675-691.
- R. Venkataraman, (2010), “Innovative Ideas for Improving Foundry Productivity and Casting Quality”, Transactions of 58th IFC, pp-113-122.
- R. Jayachitra and P. S. S. Prasad, (Apr. 2010) “Design and selection of facility layout using simulation and design of experiments”, Indian Journal of Science and Technology, Vol. 3 No. 4, 437-446.
- W. Wiyaratn, A. Watanapa, (2010 )“Improvement Plant Layout Using Systematic Layout Planning (SLP) For Increased Productivity” World Academy Of Science, Engineering And Technology 48,
- Prof. Girish Pude, Prof. G. R. Naik and Dr. P. G. Naik, (2012), “Application of Process Activity Mapping and Waste Reduction in Foundry Industry”, International Journal of Modern Engineering Research, vol.2, Issue 5, pp-3482-3496, ISSN-2249-6645.
- Bhim Singh, Suresh K. Garg, and Surrender K. Sharma, (2011) “Value stream mapping: literature review and implications for Indian industry” Int J Advanced Manufacturing Technology 53, 799–809.
- Pramod P. Shewale, Manmath S. Shete, Prof. Dr. S. M. Sane, (2012) “Improvement In Plant Layout Using Systematic Layout Planning (SLP) For Increased Productivity” International Journal Of Advanced Engineering Research And Studies EISBN2249–8974
To view full paper, Download here .
To View Full Paper
For authors
Author's guidelines Publication Ethics Publication Policies Artical Processing Charges Call for paper Frequently Asked Questions(FAQS)Publishing with
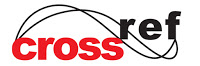
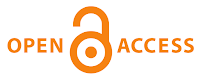
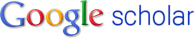
