Colour Detection of an Object in an Assembly Line
Shubhika Giri, Aditya Revoo
International Journal of Computational and Electronic Aspects in Engineering
Volume 3: Issue 3, August 2022, pp 44-46
Author's Information
Shubhika Giri1
Corresponding Author
1Student, Department of Robotics and Automation Engineering, USICT, Guru GobindSingh Indraprastha University, Delhi, India
shubhika.00916418720@ipu.ac.in
Aditya Revoo2
2Student, Department of Robotics and Automation Engineering, USICT, Guru GobindSingh Indraprastha University, Delhi, India
Abstract:-
Nowadays, vision systems are used in many things to run the industries error free with great accuracy, and for that, image processing is one of the keys that is used in this paper. This paper focuses on product differentiation using the colour detection method in real time with the help of MATLAB software. First task is to take snapshot from the web cam and convert that RGB image into HSV image, in this HSV image plays a vital role in colour description as it makes easier, they need luminous of the image. Threshold value of HSV used for differentiating colour, after applying the threshold values some of the corrections are done for avoiding any kind of error like erosion, dilution and holes.Index Terms:-
Image Processing, Colour Detection, MATLABREFERENCES
- Kazemi, S., & Kharrati, H., Visual processing and classification of items on moving conveyor with pick and place robot using PLC. Intelligent industrial systems, 3(1), 15-21, 2017.
- Chen, L., Yang, H., & Liu, P., Intelligent robot arm: Vision-based dynamic measurement system for industrial applications. In International Conference on Intelligent Robotics and Applications (pp. 120-130), 2019. Springer, Cham.
- Thiyagarajan, K., Meenakshi, R., & Suganya, P. (2016, March). Vision based bottle classification and automatic bottle filling system. In 2016 International Conference on Advances in Human Machine Interaction (HMI) (pp. 1-3). IEEE.
- Jørgensen, T. B., Jensen, S. H. N., Aanæs, H., Hansen, N. W., & Krüger, N. (2019). An adaptive robotic system for doing pick and place operations with deformable objects. Journal of Intelligent & Robotic Systems, 94(1), 81-100.
- Raghunandan, A., Raghav, P., & Aradhya, H. R. (2018, April). Object detection algorithms for video surveillance applications. In 2018 International Conference on Communication and Signal Processing (ICCSP) (pp. 0563-0568). IEEE.
- Dubey, A. P., Pattnaik, S. M., & Saravanakumar, R. (2016). Control and Operation of 4 DOF Industrial Pick
To view full paper, Download here
To View Full Paper
For authors
Author's guidelines Publication Ethics Publication Policies Artical Processing Charges Call for paper Frequently Asked Questions(FAQS) View All Volumes and IssuesPublishing with
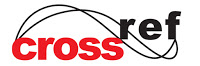
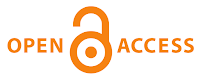
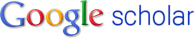
